A coaming, upon which a dogger can later be fitted, was constructed on either side of the companionway opening. Because of the extreme curve, I used bendply to laminate pieces out of which the final shape was planed.
Jahazi
a Didi 34 being built by her owner in his spare time. This blog gives a chronological history of the building process.
Jahazi
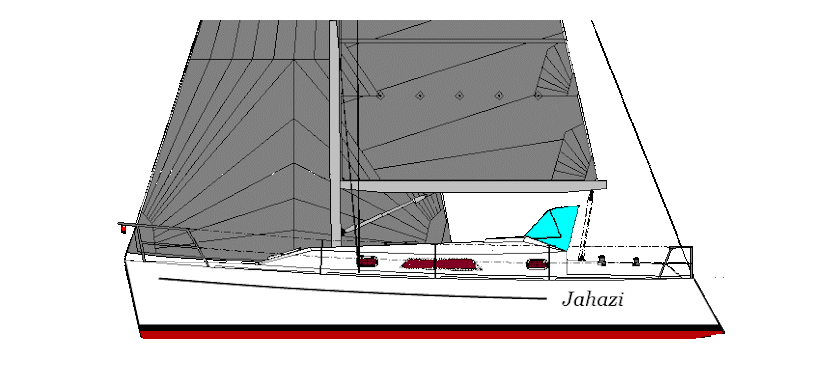
Introduction
"If you want to build a ship, don't drum up people to collect wood and don't assign them tasks and work, but rather teach them to long for the endless immensity of the sea"
Antoine de Saint-Exupery
Pages
Monday 16 March 2020
Tuesday 18 February 2020
Wednesday 4 December 2019
Roof doublers
The cabin roof needs to be strengthened in areas where there are load bearing deck equipment. This is done by adding doublers on the inside. I used wood supports to keep them in place until the epoxy set.
Wednesday 20 November 2019
Hatch frames
The deck hatches are to be mounted on a flat surface. Therefore I had to make frames with a curved edge on the one side and a flat edge on the other. I made a jig using a long batten with a length similar to the radius of the deck crown to cut the curved sides of the timber with a router.
Tuesday 22 October 2019
Companionway door and sliding hatch
The boat plans specify a simple Plexiglas sliding hatch. However I decided to go for a more traditional look with a hatch build from marine ply and teak.
The companionway frame and hatch slides were also made using teak.
Thursday 25 April 2019
Companionway ladder
The boat plans do not include a plan for the construction of the companionway ladder. Since the dimensions for each boat will be different, I had to design my own using ladder design guidelines such as the optimum step depth, distances apart and the angle of the ladder. Using the program "Sketchup" I came up with the following.
![]() |
My plan with dimensions |
![]() |
How its should look |
The end product |
Wednesday 17 April 2019
Fiberglass sheathing of the deck
Although the building plans do not specify fiberglass sheathing of the deck, I have decided to do sheathing not realizing the amount of work involved. It will however increase the strength and stiffness of the deck, provide added impact and abrasion resistance and an overall better resistance to wear.
To do the sheathing dry fiberglass cloth was positioned on the surface and epoxy poured directly onto the fabric in small puddles and the epoxy was then worked into the fabric using a plastic squeegee and/or foam roller to remove trapped air. When tacky another layer of white epoxy was applied and Peel Ply applied on the wet epoxy.
The use of Peel Ply in the sheathing process is extremely important. The closely woven nylon cloth of the Peel Ply is a release fabric to which epoxy will not adhere and is applied as the last layer of the sheathing process. When the Peel Ply is removed at a later stage, the textured surface will need no or only a little sanding thus allowing further layers of glass/epoxy, fairing compounds or coatings to be applied.
To do the sheathing dry fiberglass cloth was positioned on the surface and epoxy poured directly onto the fabric in small puddles and the epoxy was then worked into the fabric using a plastic squeegee and/or foam roller to remove trapped air. When tacky another layer of white epoxy was applied and Peel Ply applied on the wet epoxy.
The use of Peel Ply in the sheathing process is extremely important. The closely woven nylon cloth of the Peel Ply is a release fabric to which epoxy will not adhere and is applied as the last layer of the sheathing process. When the Peel Ply is removed at a later stage, the textured surface will need no or only a little sanding thus allowing further layers of glass/epoxy, fairing compounds or coatings to be applied.
The fiberglass is white cloth when dry. |
but becomes transparent when wet-out with the epoxy |
The final layer of epoxy is covered with peelply |
The peelply provides a rough surface for bonding of the final layer of paint. |
Wednesday 5 December 2018
Cabin and deck fairing
Friday 2 November 2018
Cabin top
After spending a month touring Namibia by 4x4, I was back building Jahazi. Next the cabin top had to be done. Before laminating the cabin top, the cabin top beams must be fitted. These were already done in 2017, so I could start straight-away. The cabin top is of 12 mm ply and because of the curvature of the roof must be laminated from 2 layers of 6 mm ply. The easiest way of doing this is by using 500 mm ply strips across the width. When working alone these are more manageable than larger pieces.
Thursday 12 July 2018
Coaming constuction
![]() |
coaming at 55 degrees (not my build) |
Subscribe to:
Posts (Atom)